Meet the Team: Kurt Puffpaff
Kurt Puffpaff ROCKS! Though in Kurt’s case, we mean that quite literally. A musician and music aficionado, Kurt plays guitar, sings, and is a huge fan of ‘70s rock bands like AC/DC, Styx and Led Zeppelin. He also writes and records his own original tunes, played on his favorite Birdseye Maple Les Paul guitar. Besides his love for music, Kurt is an avid outdoorsman and a die-hard Kansas City Chiefs fan.
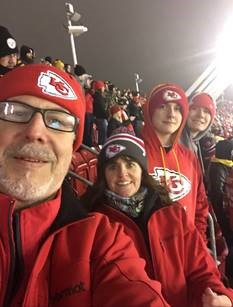
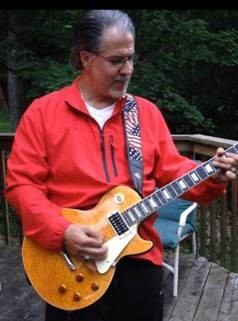
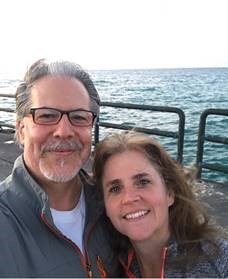
Born and raised in Charlevoix, Michigan, Kurt has moved around the Midwest for his career before returning to his hometown a few years ago and settling with his wife Diane and their four sons, aged from 11 to 22.
Kurt is currently the National Sales Manager for A.L.P.’s custom optical products, but he has been in the lighting industry since 1993. He started his career as a territory manager for LexaLite (now part of A.L.P.) where he learned the business from the ground up, even delivering a few orders by truck when the business depended on it. Drawing on his decades of expertise in injection molding, Kurt can answer almost any molding question that comes his way. You are also invited to pick his brain on classic rock, football, or hunting.
A.L.P., Charlevoix, injection molding, Kansas City Chiefs, Kurt Puffpaff, Les Paul Guitar, LexaLite, musician, National Sales Manager, outdoorsman
Press Release: A.L.P. Produces PPE Face Shields for COVID-19 Health Care Workers
Joining the fight against the COVID-19 pandemic, the injection molding team at A.L.P. LexaLite’s Charlevoix, MI facility mobilized to design and manufacture Personal Protective Equipment (PPE) face shields for front-line health care workers. They rapidly reorganized tooling and manufacturing functions to support this critical need, and they expect to have the first production models coming off the presses within days.
The company was initially approached by Charlevoix Hospital, looking for PPE. While primarily a manufacturer supplying components for lighting fixtures, A.L.P. has several customers in the health care sector. The team drew on its knowledge of health care requirements and standards to quickly design and tool the face shields in an unprecedented 10-day turnaround.

When in full production, A.L.P. can produce approximately 1400 face shields per day, and they plan to sell them at cost. “We will make them as long as they are needed,” states Steve Brown, CEO.
“This is one scenario I didn’t see coming,” Brown adds. “The COVID-19 crisis is tragic, yet it shows us what we can accomplish together when needed,” he observes. A.L.P. is not alone, as manufacturers all over the country are making similar efforts.
The A.L.P. face shield has some unique features. The plastic shield snaps onto a headband, and the shield is disposable. So, the caregiver can use the same headband throughout the day and simply snap on a new shield for each patient.
A.L.P. continues to operate during this crisis as an Essential Business, supplying into vital infrastructure such as construction, health care, transit, and government. The company has adjusted its practices, with the health and safety of employees, families, and communities as a top priority. The A.L.P. staff is working remotely when possible. All manufacturing locations have implemented additional measures to ensure safe distancing of employees, such as adjusting schedules, spacing equipment, and reorganizing meeting and break room spaces.
Charlevoix, COVID-19, disposable shield, Essential Business, headband, Health Care Workers, injection molding, LexaLite, Personal Protective Equipment, PPE Face Shields, tooling
Press Release: A.L.P.’s Charlevoix Facility Achieves ISO Certification
(Niles, IL) -A.L.P. is pleased to announce that our Charlevoix, MI facility has been certified to ISO 9001:2015 by DNV GL. A.L.P.’s Dickson, TN facility has been certified to 9001:2015 since November 2018. A.L.P. has had a long-established Quality Management System, and these certifications affirm our commitment to effective manufacturing and business practices. “We welcome new and existing customers to audit our facilities,” offers Tom Barnes, VP and Business Unit Manager. “We hope these certificates offer an extra measure of confidence in our abilities,” he adds. A.L.P.’s Charlevoix and Dickson facilities produce LexaLite® brand injection molded components. A.L.P. has also significantly expanded its injection molding capacity in the Monterrey, Mexico plant.
A.L.P. LexaLite is an industry-leading provider of injection molded components in thermoplastic and optical silicone. Long recognized for designing and manufacturing innovative optical lighting components, A.L.P LexaLite also serves markets such as Medical, Automotive, Signage, Point of Purchase, Electronic Equipment, Appliance, and Mass Transportation.
A.L.P.’s team of experts provides specialized services from product design and engineering to tooling and prototyping, product testing and contract assembly. Production capabilities include press sizes ranging 88-1650 tons and industry-leading capabilities in secondary operations such as UV coating and laser cutting. Committed to innovation and responsive to market requirements, A.L.P. LexaLite also offers unrivaled capacity in optical silicone injection molding and edgelit injection molding.
A.L.P. is an international leader in the design, manufacturing, and distribution of lighting components and components for other technical industries. We offer the industry’s most comprehensive line of products for OEMs and the aftermarket. For custom projects, our unique “360° Solutions” suite of custom services enables us to collaborate with customers at every stage of a product’s life cycle. Our core commitment is to provide superior service and product performance to every customer.
Charlevoix, Edgelit, injection molding, ISO 9001:2015, ISO Certification, MI, Optical Silicone, Press Release, Thermoplastics
A.L.P. Adds New Edgelit Panel Equipment
A.L.P. Lighting Components, manufacturer of LED lighting components and fixture kits, has added to its industry-leading capacity to produce molded edgelit lighting panels. Taking advantage of Rambus closing its Brecksville, OH facility, A.L.P. purchased a 1,650-ton press, molds and other equipment to be installed in its Charlevoix, MI plant. A.L.P.’s LexaLite® brand has been at the forefront of edgelit technology for more than three decades, with preeminent production resources, expertise, and mold inventory. A.L.P. is currently the only North American manufacturer capable of injection molding both 1’x4’ and 2’x2’ edgelit panels.
By using standard molds with custom inserts, A.L.P. can quickly and inexpensively manufacture prototypes and low-volume production runs. Standard sizes include 48” x 12”, 24” x 12”, 24” x 8” and 24” x 24”. For large production orders, A.L.P.’s expert tooling and engineering teams can develop high volume tooling based on customers’ specifications for size, light source, light output pattern, thickness, and aesthetics. A.L.P. also has in-house CAD modeling and photometry testing resources.
Edgelit panels have gained increasing popularity for maximizing and retrofitting in-ceiling lighting. Flat edgelit panels are very thin, offering the versatility of mounting on a variety of surfaces including walls and ceilings, as well as providing the option of cable suspension. They are often considered “shadowless” because they produce broad, even light.
“We work closely with customers to meet all requirements for performance, cost, and speed to market,” states Tom Barnes, Vice President and Business Unit Manager for A.L.P. LexaLite. “By further investing in edgelit molding technology, A.L.P. can respond even more quickly to the needs of a rapidly changing lighting marketplace,” Barnes concludes.
Charlevoix, Edgelit, equipment, injection molding, LED, LexaLite, lighting panels, retrofit, shadowless, standard sizes, tooling